What You Need to Know About Industrial Pipe Coating
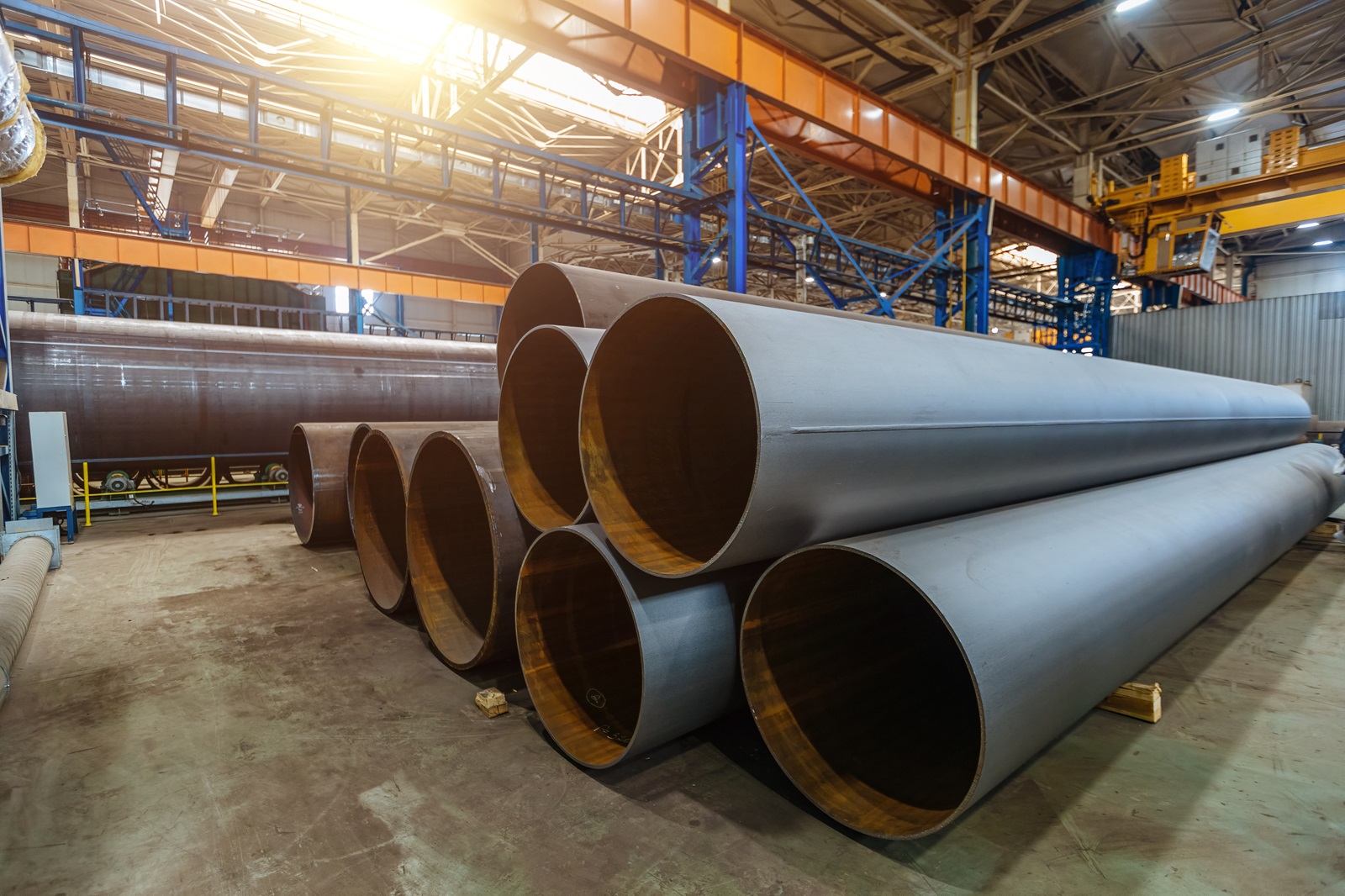
Sometimes short-term gains can lead to long-term pain. Relying on unprotected bare metal pipes for your industrial process or transfer project can save you money at installation time, but may end up costing you more in maintenance and repairs down the line. Unprotected pipes are susceptible to corrosion, abrasion, flow inefficiencies, and even catastrophic failure.
In this blog, we take a look at why leading operators rely on comprehensive pipe coating for their critical infrastructure. We’ll review the many benefits pipe coatings offer over the lifespan of your project, take a closer look at coating options, and consider how to choose the right treatment for your pipes.
Why Choose Industrial Pipe Coating?
Metal piping is used in almost all industrial processes and wherever large amounts of oil, chemical products, or other liquids need to be transferred over distance. Strong and adaptable to almost any application, metal piping does come with some significant disadvantages.
Whenever bare metal piping comes in contact with moisture or caustic or oxidizing chemicals, it becomes susceptible to corrosion. Left unchecked, pipe corrosion can lead to leaks, pipe failure, or contamination of your fluids.
In many cases, it can significantly shorten the use life of your piping infrastructure. Damaged pipes often require expensive and unplanned downtime for maintenance, replacements, and repairs, while posing a potential safety risk to your staff and customers.
Tough, durable coatings provide a proactive solution to pipe corrosion. Applied to the outside or inside of piping, pipe coatings help prevent pipe corrosion due to environmental exposure or contact with harsh fluids being carried within the pipe. In fact, studies have shown that applying a coating to bare metal piping can extend its life by anywhere from 50% to 85%.
The right coating will also prevent contamination of your product and can even improve flow within the pipe by reducing friction and preventing build-up or blockages.
Benefits of Pipe Coatings for Your Industry
Effective pipe coatings extend the life of your infrastructure and improve flows within pipes. They also limit planned and unplanned downtime. While coating pipes increases your up-front investment, it’s money well spent to ensure long-term value and return on investment.
Pipe coating also delivers specific benefits to a wide range of industries. Take a look at the following table to find out more.
Pipe Coating Benefits by Industry | |
---|---|
Industry | Benefits |
Oil & Gas Production and Transfer |
|
Power Plants |
|
Food and Beverage Processing |
|
Chemical Processing |
|
Marine and Offshore |
|
Coating Types and Applications
Industrial pipe coatings are applied to both the inside and outside of a pipe, depending on the application and the level of protection required.
External Coatings
External coatings protect pipes from external environmental factors such as extreme temperatures, corrosion, and chemical exposure. They also help to prevent abrasion and other types of mechanical damage to pipes.
Commonly used external coating materials include:
- Polyethylene: Used widely with underground and underwater pipes for protection against moisture and salt.
- Epoxy: Tough and highly resistant to chemicals. Often used in harsh operating environments.
- Fusion-bonded epoxy: A chemically-bonded epoxy coating valued for its durability and excellent adhesion properties.
- Coal tar enamel: Typically used in harsh corrosive operating environments, especially to protect marine undersea pipelines.
Internal Coatings
Internal coatings or linings are designed to protect the pipe’s interior from corrosion and to improve flow efficiency by reducing friction and preventing material buildup.
Commonly used internal coating materials include:
- Cement mortar lining: Widely used in large water and sewage pipes to prevent corrosion and waste buildup.
- Epoxy linings: Offers corrosion protection and chemical stability. Commonly used in pipelines carrying potable water as well as oil and gas.
- Polyurethane linings: Provide excellent chemical resistance and are often used in aggressive fluid environments.
- Coal tar enamel: Used to protect pipe interiors from corrosive chemicals and to maintain flow in raw water and wastewater piping.
The following table summarizes the suitability of common pipe coating materials for different applications:
Coating Materials by Application | ||||||
---|---|---|---|---|---|---|
Coating Material | Corrosive | Abrasive | Hi-Temp | Low-Temp | Hi-Pressure | Insulating |
Epoxy Coating | ✔️ | ➖ | ✔️ | ✔️ | ✔️ | ❌ |
Polyurethane Coating | ✔️ | ✔️ | ❌ | ✔️ | ➖ | ❌ |
Zinc-Rich Coating | ✔️ | ➖ | ✔️ | ✔️ | ✔️ | ❌ |
Coal Tar Enamel | ✔️ | ✔️ | ➖ | ✔️ | ✔️ | ❌ |
Fusion-Bonded Epoxy | ✔️ | ✔️ | ✔️ | ✔️ | ✔️ | ❌ |
Polyethylene Coating | ✔️ | ✔️ | ❌ | ✔️ | ➖ | ✔️ |
Cement Mortar Lining | ✔️ | ❌ | ❌ | ✔️ | ❌ | ✔️ |
Polyurethane Lining | ✔️ | ✔️ | ❌ | ✔️ | ➖ | ✔️ |
Intumescent Coating | ❌ | ❌ | ✔️ | ❌ | ❌ | ❌ |
Vinyl Ester Coating | ✔️ | ➖ | ✔️ | ✔️ | ➖ | ❌ |
Both internal and external coatings must be matched to your material, application, and operating conditions. While many companies offer pipe coating services, it’s important to work with an experienced provider like MultiService Industrial to ensure you get the right coatings and linings to meet your specific needs.
How to Choose the Right Coating for Your Application
The right coating for your pipes can improve safety and efficiency and dramatically increase your pipe’s use life. The wrong coating could mean expensive pipe replacements or remediation measures down the line. Here are six key steps to make sure you get the coating you need.
Coating Selection Checklist | |
---|---|
1. Assess your operating conditions |
|
2. Determine mechanical stress levels |
|
3. Consider industry-specific requirements |
|
4. Evaluate cost vs. longevity |
|
5. Consult with an expert |
|
6. Ensure compliance with industry standards |
|
Maintenance and Inspection
While an effective pipe coating will reduce your overall maintenance burden, it is not a substitute for performing regular scheduled inspections and maintenance on your equipment. To get the maximum benefit from your industrial coating, it’s important to catch any problems early.
It’s also essential to understand the conditions your equipment will be operating under. The wrong coating for the conditions will cause your equipment to underperform.
By understanding the characteristics of the fluids you are transporting and the conditions you operate in, an experienced pipe coating supplier like MultiService Industrial will be able to customize a coating solution to fit your needs.
MultiService Industrial: We’ve Got You Covered
At MultiService Industrial we understand that cost is not the same as value. We also know that cutting up-front expenses by skimping on protection can end up costing you more in the long run. That’s why we take the time to understand your specific process needs and budgetary constraints and offer coating solutions that maximize long-term value.
Talk to us about your pipe corrosion challenges. We pride ourselves on offering coatings ideal for any application or operating environment, and we believe in “Doing It Right” up-front, so you can enjoy both peace of mind and the long-term benefits of investing wisely.
Contact us today to find out how we can help you succeed in the long term, or click below to learn more about our pipe-coating services.