How Long Does Pipe Coating Last?
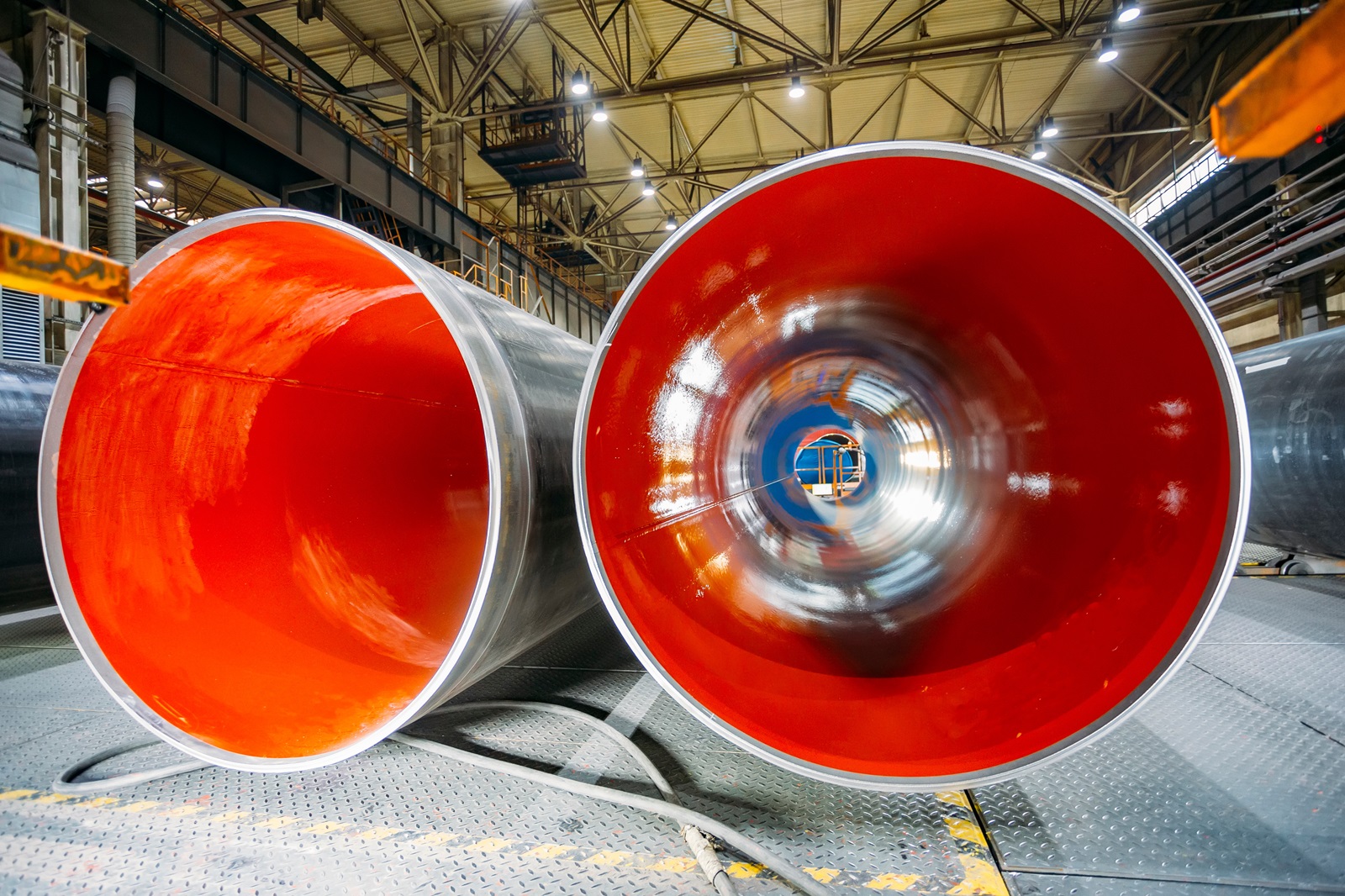
Pipe coating can add to the upfront cost of your project’s procurement, engineering, and installation process, but delivers value down the line in the form of lower maintenance costs, improved flows, and other efficiencies.
It’s important to understand how long your pipe coating is expected to last to calculate the expected return on your investment in pipe treatments.
Keep reading as we consider how your pipe coating’s longevity affects the costs, efficiency, and overall return on investment in your project’s flow equipment infrastructure, as well as the benefits of going with a reputable coatings provider like MultiService Industrial.
How Longer-Lasting Pipe Coating Benefits You
Choosing the right pipe coating to protect your piping for longer benefits you and your operation in five ways:
- Operational cost savings: Longer-lasting coatings reduce the need for frequent maintenance, repairs, and replacement over time, helping to limit your labor and parts replacement bills and other lifetime operational costs.
- Limited downtime: Effective coatings limit corrosion, cracks, and leaks, preventing catastrophic pipe failure. That means less expensive pipeline downtime over the life of your project.
- Improved safety: By protecting piping from impacts and abrasions, limiting the time spent accessing pipes in hazardous environments, and preventing catastrophic failures, effective coatings protect workers, customers, and local communities from harm.
- Better flows: Depending on the fluids you are transporting, internal pipe coatings can reduce friction and deposits, improving pumping efficiency and throughput.
- Predictability: Knowing how long your pipes will be protected allows for better budgeting on maintenance, repair, and insurance costs.
Taken together, these factors provide both added project value and indirect savings as a result of your upfront investment in pipe coatings.
What Affects How Long Your Coating Will Last?
Pipelines and fluid-handling infrastructure operate in challenging, often harsh, conditions. While results will vary from project to project, there are two key factors determining how well a coating is likely to perform in a given setting.
1. Type of Coating Material
Not all coatings are created equal. Individual materials provide varying levels of protection against different types of stressors.
For example, epoxy coatings provide excellent chemical resistance and are commonly used in pipelines handling harsh fluids. However, polyurethane coatings offer better abrasion resistance and are often chosen for environments where pipes face high levels of physical wear and tear.
The following table lists 10 types of commonly used coatings, the type of protection they are designed to provide, and their typical application lifespan under ideal conditions.
Coating | Type of Protection |
---|---|
Epoxy coating | Corrosion and chemical resistance |
Polyurethane coating | Abrasion resistance and chemical protection |
Zinc-rich coating | Corrosion protection, galvanic protection |
Coal tar enamel | Corrosion resistance in marine and subsurface environments |
Fusion bonded epoxy (FBE) | Corrosion resistance, chemical, and mechanical protection |
Polyethylene coating | Corrosion and abrasion resistance |
Cement mortar lining | Corrosion resistance in water and sewage pipes |
Polyurethane lining | Chemical resistance and abrasion protection |
Intumescent coating | Fire resistance |
Vinyl ester coating | Chemical and high-temperature resistance |
2. Operating Conditions
Pipelines and flow-handling equipment — and their coating are typically exposed to a wide range of environmental conditions. These include:
- Temperature fluctuations: Expansion and contraction of piping materials due to extreme temperature variations can cause coatings to crack or peel.
- UV exposure: For pipes exposed to sunlight, UV radiation can degrade many coatings over time.
- Chemicals: In industrial and chemical processing environments, pipes are often required to carry caustic or corrosive agents that can shorten a coating’s life.
- Moisture and salt: Marine and coastal environments accelerate corrosion due to high humidity and salt exposure, requiring robust coatings like coal tar enamel or epoxy.
- Abrasion and mechanical shock: Bumps, knicks, and wear and tear can shorten the use lives of many kinds of coating.
It’s worth consulting with a pipe coating expert like MultiService Industrial about the best coating material for your application and operating environment.
Maximizing Pipe Coating Lifespan
How can you get the most out of your investment in a pipe-coating solution? Two factors play a role in determining how long your pipe coating is likely to last: expert application and ongoing inspections and maintenance.
1. Application Expertise
Correct application is the first and most important step in ensuring a coating’s durability. And, it’s more than a one-shot job. Experienced coatings suppliers know that surface preparation is just as important as the coating material itself.
Even the most advanced coating can fail if applied to a poorly prepared surface. That’s why at MultiService Industrial we take extra care to ensure your pipes are properly cleaned by sand-blasting or chemical application to ensure optimal coating adhesion.
Once the pipe surface is prepared, the coating should be applied at the correct thickness, and (depending on the coating material) that it be properly cured. This is critical to preventing the coating from blistering, cracking, or peeling.
Improperly applied coatings can cost you plenty in extra maintenance, patching, and recoating over the lifespan of your project. That’s why you need to trust a reputable, experienced provider with the job.
2. Ongoing Maintenance and Inspections
As any structural engineer knows, maintenance is a continuous process. Coating solutions, no matter how well applied, will always degrade eventually. Regular inspections, touch-up applications, and re-coating can significantly extend your coating’s use life.
It pays not to skimp on internal and external pipe inspections. This is particularly important when pipes are exposed to harsh or potentially hazardous conditions.
Identifying signs of wear, such as thinning, cracking, and blistering, allows issues to be tackled early before they can develop into major problems. Minor touch-ups limit the need for major maintenance interventions and are easier and cheaper to apply than a full recoating.
Expected Lifespan of Common Pipe Coatings
The lifespan of a given pipe coating naturally depends on the application, operating environment, and how well your coatings are applied and maintained. That makes it hard to predict lifespans accurately. The coating might perform differently in mild, temperate conditions versus extreme heat and cold.
Also remember, a coating that improves flow efficiency and protects effectively for only 10 years, or one that delivers excellent fire protection for just seven, might be a better investment for your application than an alternative that lasts longer but does not perform as well.
In broad terms, the following estimated lifespan consideration may be expected to apply.
- Highly specialized products like fire-resistant intumescent coatings last significantly shorter than coatings designed primarily with protection in mind.
- Epoxies, vinyl ester, and polymer-based coatings typically last between 10 and 20 years when used for the right applications and in the environment for which they were designed.
- Inert coatings like zinc-rich treatments, coal tar enamel, and concrete lining can be expected to last much longer, often between 15 and 25 years, depending on the application type.
In reality, lifespans will vary widely depending on the exact coating formulation used, how well the pipe surface was prepared, maintenance levels, the environment the pipe is used in, and the type of fluid it is carrying.
Why Consult with an Expert?
Many companies offer pipe coatings services, often with cut-price services and one-size-fits-all solutions. However, there is no substitute for experience when it comes to adapting your coating election to specific applications and operating environments.
A specialist provider like MultiService Industrial has the deep knowledge you need to assess a project and identify the right solution — whether it’s a chemical processing facility, a power plant, or a marine pipeline — and the skills to prepare your pipes and apply your chosen coating correctly every time.
For long-term, high-value projects, it makes little sense to skimp on protection upfront. Investing in quality coatings is not just a smart operational strategy, it’s an investment in the long-term success of your project.
Multiservice Industrial: We’ve Got You Covered
At MultiService Industrial, we believe in “doing it right”, the first time, every time. Our customers trust us to deliver the coating they need on time and within budget, with perfect application to guarantee performance and longevity in even the harshest operating environments.
If you’re an engineer looking at a project timeline from 10 to 30 years, we can provide the right coating for your application over the long haul. By investing in the right materials today, you’ll benefit from improved flows and reduced operating expenses throughout your project.
Talk to us about your goals and maintenance challenges. We’ll recommend the right internal or external coating for the job, and ensure it’s applied efficiently and effectively for long-term value and maximum return on investment.
Contact us to find out how MultiService Industrial can help you succeed in the long term, or click below to schedule a free consultation today.