Does Heat Trace Require Insulation?
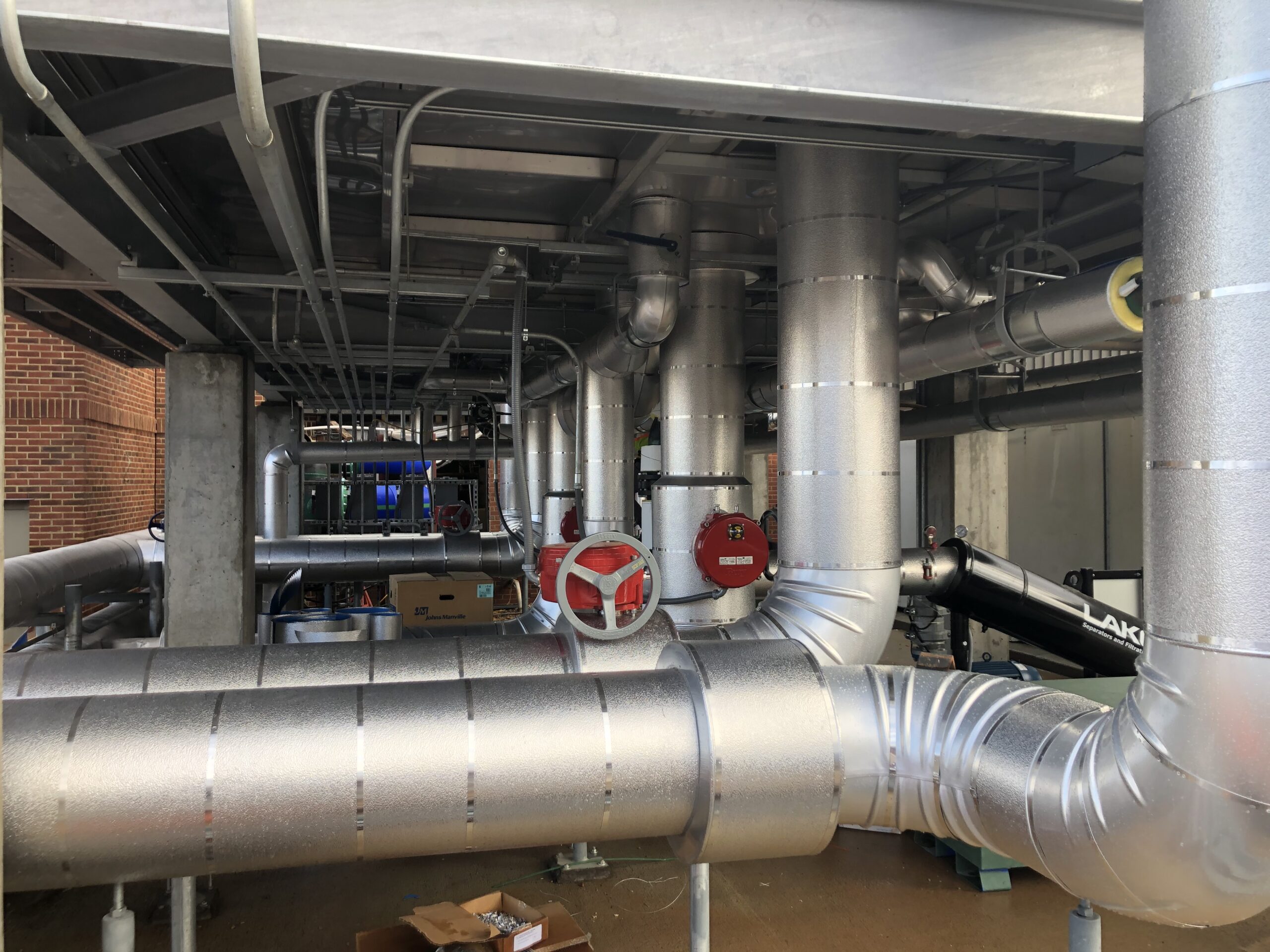
Like peanut butter and jelly and mac and cheese, some things just work better together. The same goes for heat tracing and pipe insulation. This dynamic duo combines to deliver maximum heating efficiency to keep your fluids moving.
In this blog, we break down how wire and wrapping combine in this classic industrial match-up.
It’s a Wrap: Heat Tracing and Insulation
Heat tracing is used widely to warm exposed piping to prevent transported materials from freezing, congealing, or condensing when ambient temperatures drop. It’s essential to keeping gasses and liquids flowing smoothly.
However, using heat tracing without also insulating the piping makes little sense. It’s a bit like running a bath without first putting in the plug. You could do it, but it would waste a lot of water.
Similarly, an insulation system is essential to keeping heat from heat tracing cable where it needs to be — right next to the pipe. Without appropriate insulation, heat provided by the tracing is rapidly lost to the environment, rather than working to heat the pipe itself.
Benefits of Using Heat Tracing with Insulation
Let’s break down some of the key benefits of using heat tracing with insulation:
1. Optimize System Efficiency
By reducing heat loss to the environment and reducing energy spikes by maintaining temperature levels, insulation helps ensure your heat tracing works at peak efficiency. That means lower energy bills and a smaller carbon footprint to reach the same heating goals.
2. Maintain Desired Temperatures
Maintaining pipe at a desired temperature supports optimum flow rates for whatever material you are transporting with lower viscosity and less condensation. You’ll see improved productivity, especially during harsh weather events, and lower startup costs when you switch your heat tracing system on.
3. Protect Pipes from Freezing
Most importantly, you will protect your pipes carrying water and other materials prone to freezing at atmospheric temperatures. Freeze protection allows you to maintain flow in even the harshest conditions. It also reduces the need for urgent repairs due to leaks and burst pipes, offering large potential savings on your maintenance bill.
4. Enhance Equipment Longevity
By reducing energy spikes and the overall temperature that heat tracing wire needs to cover, effective insulation increases the longevity of your heat tracing system, offering a better return on investment for your pipe-protection infrastructure.
Optimizing Heat Trace Insulation
Determining the ideal type and thickness of insulation to use with your heat tracing system is a complex decision based on detailed knowledge about heat transfer and the properties of insulating materials.
For optimum efficiency and return on investment, it’s best to consult a heat tracing equipment expert like MultiService Industrial. A qualified heat tracing professional can determine the right material and thickness for your insulation by looking at:
Pipe Material and Thickness
It’s important to consider both the material used in piping as well as the thickness of the pipe wall to determine how much heat tracing capacity and insulation will be required to reach and maintain the desired temperature.
Ambient Temperature Range
What is the ambient temperature range that your pipes will be exposed to? Very cold conditions will require increased insulation to deliver the same efficiency for a given heat trace input.
Desired Temperature Maintenance Level
What is the desired temperature required to keep your transported material flowing smoothly? Different materials from gasses to oil tar will require different amounts of insulation to ensure an efficient flow at a given ambient temperature.
The following table illustrates the steps a MultiService heat tracing expert will take to determine the right insulation type and thickness for your project’s specific needs.
Key Steps in Determining Insulation Solutions for Heat-Traced Piping |
---|
1. Determine Heat Loss |
Calculate the heat loss per unit length of pipe using scientific formulas and specialized software. Factors to consider include:
|
2. Select Insulation Material |
Choose insulation with a thermal conductivity suitable for the application, ensuring that it:
|
3. Set Heat Tracing Capacity |
Ensure the heat tracing system can supply enough heat to maintain the desired pipe temperature. This involves:
|
4. Adjust for Safety Margins |
Add a safety buffer to account for unforeseen conditions such as colder-than-expected temperatures or poorer performance by aging insulation materials. |
5. Verify System Performance |
Conduct testing to make sure that insulation and heat tracing work together effectively under the expected conditions. |
Comprehensive Pipeline Protection
At MultiService Industrial, we are committed to “Doing It Right” every time. Our team of skilled, experienced engineers and technicians are equipped to offer end-to-end pipeline protection services from heat tracing to insulation to coating. Why take the risk with yet another contractor when you can have one supplier who understands how all the pipe protection parts fit together?
We know that no two pipeline projects are the same, so we tailor our services to the specific needs of your project, rather than offering off-the-shelf solutions. We’ll provide the best match of insulation and heat tracing to deliver ultimate energy efficiency, maximum flow performance, and long-term pipeline protection.
Click below to get started with a free quote or schedule your complimentary consultation.