Heat Trace Design Guide: Avoid Costly Mistakes with This Guide
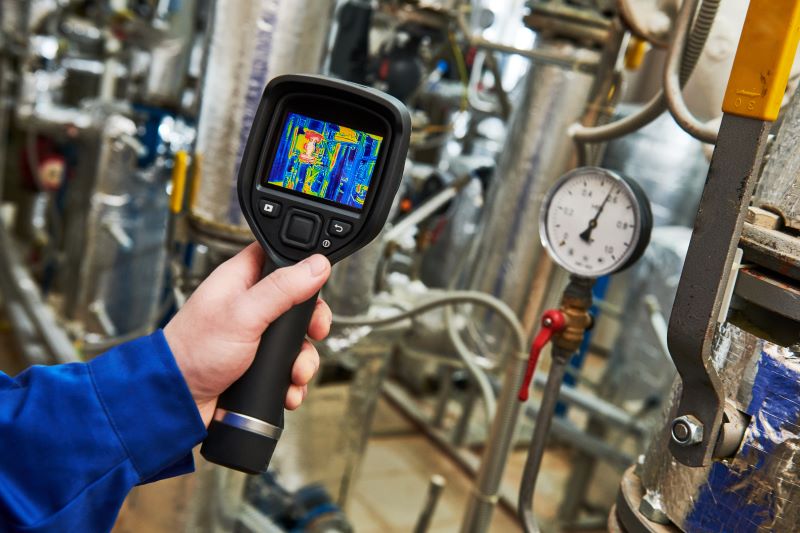
- What is Heat Tracing?
- Benefits of Proper Heat Trace System Design
- Types of Heat Tracing Systems
- Key Considerations in Custom Heat Tracing Design
- Key Components of a Heat Trace Systems
- How MultiService Industrial Designs Heat Trace Systems
- Heat Tracing Installation
- Maintenance and Troubleshooting
- The Importance of Partnering With an Expert Contractor
- Why Choose MultiService?
- Industries We Serve
- Ready to Optimize Your Heat Trace System?
Picture this: It’s a frigid winter morning, and your production line grinds to a halt because of a frozen pipe. Not a great way to start the day, right? That’s where heat tracing comes in. It’s like a warm hug for your pipes and critical equipment, keeping things flowing smoothly no matter the weather.
Heat tracing is a critical component in industrial operations, providing temperature control that keeps systems functioning smoothly and safely. Whether you’re preventing pipes from freezing, maintaining specific process temperatures, or ensuring safety in extreme conditions, a well-designed heat trace system can make a significant difference.
At MultiService Industrial, we’re passionate about designing and installing heat trace systems that provide reliable, efficient, and safe temperature control for industrial facilities just like yours. In this guide, we’ll dive into everything you need to know about heat tracing and what it is, its benefits, the risks of working with an unskilled contractor, and why MultiService Industrial is your ideal partner for designing and maintaining these vital systems.
What Is Heat Tracing?
Heat tracing involves applying a controlled heat source to pipes, vessels, and equipment to maintain or increase their temperature. This process is especially essential for industries working in cold climates or handling materials that need precise temperature control. Whether it’s freeze protection or keeping materials at the ideal temperature, heat tracing ensures smooth operation year-round.
Benefits of Proper Heat Trace System Design
A properly designed heat trace system can provide a variety of benefits:
- Cost Savings: By minimizing energy waste, heat tracing systems can reduce operating costs while preventing expensive damage due to freezing or overheating.
- Enhanced Reliability: A well-planned heat trace system reduces downtime, ensuring consistent operation across your processes.
- Improved Safety & Compliance: Designing systems with safety standards in mind helps protect your team, equipment, and facilities, ensuring compliance with industry regulations.
Why Heat Tracing Is Essential in Industrial Settings
- Preventing Downtime: Frozen pipes and equipment can cause costly production delays. Heat tracing ensures systems continue running smoothly, even under the harshest conditions.
- Protecting Critical Systems: Maintaining stable temperatures for sensitive equipment helps prevent degradation and ensures optimal performance.
- Saving Energy & Resources: Efficient heat tracing systems reduce energy waste, lowering operational costs and decreasing the environmental impact of your operations.
Types of Heat Tracing Systems
Electrical Heat Tracing Systems
- Self-Regulating Cables: Automatically adjust heat output based on the surrounding temperature, making them energy-efficient and adaptable to changing conditions.
- Constant Wattage Cables: Provide a consistent level of heat, ideal for situations where uniform heating is required.
- Mineral Insulated Cables: Built to withstand high temperatures, these cables are perfect for extreme conditions and offer long-term durability.
Steam Heat Tracing Systems
- Steam systems are a traditional method of heat tracing that uses steam to provide heat to pipes and vessels. While effective, steam tracing requires more regular maintenance and is typically suited for industries already utilizing steam infrastructure.
Key Considerations in Custom Heat Tracing Design
When designing a custom heat tracing system, a detailed assessment of your facility’s specific requirements is essential. Every detail, from the type of pipes to environmental conditions, plays a crucial role in creating an efficient and effective system. Below are the key considerations to guide a tailored heat tracing design:
Type, Size, and Length of Pipes
The dimensions and material of the pipes or equipment requiring heat tracing significantly impact the system’s design:
- Type of Pipes: Different materials (e.g., steel, copper, plastic) have varying thermal conductivity, affecting heat retention and energy requirements.
- Size and Length: Larger and longer pipes require more extensive heat trace coverage and may demand higher power outputs to ensure uniform heating.
- Complexity of Layout: Systems with bends, valves, or irregular shapes may need special installation techniques or additional heat tracing to ensure consistent performance.
Temperature Requirements
Maintaining the correct temperature is critical to system success. Important considerations include:
- Desired Operating Temperature: The specific temperature needed to prevent freezing or maintain process efficiency determines the heat output required.
- Heat-Up and Cool-Down Rates: Some applications demand rapid temperature changes, which must be factored into the design.
- Maximum Temperature Limits: Materials and systems often have temperature thresholds that must not be exceeded to ensure safety and longevity.
Environmental Conditions
The environment surrounding the heat trace system affects performance and durability. Factors to evaluate include:
- Ambient Temperature: Lower ambient temperatures in cold climates increase heat loss and require higher energy input to maintain desired temperatures.
- Moisture and Humidity: Wet environments may necessitate additional waterproofing or insulation to protect the system.
- Corrosive or Hazardous Conditions: Exposure to chemicals or harsh conditions may require specialized materials, such as corrosion-resistant cables or enclosures.
- Outdoor vs. Indoor Applications: Outdoor systems need protection against weather elements like rain, snow, and wind, while indoor systems might prioritize space-saving designs.
Why These Considerations Matter
Tailoring your heat tracing system to these factors ensures efficiency, safety, and longevity. By taking a comprehensive approach to design, MultiService Industrial delivers systems that minimize energy consumption, maximize reliability, and adapt to your unique operational needs.
Key Components of a Heat Trace System
- Heat Trace Cables: These are the primary components responsible for providing heat. Different cables serve specific needs, from self-regulating cables to constant wattage options and mineral-insulated varieties for demanding environments.
- Thermal Insulation: Insulation materials like fiberglass, foam, and aerogels help minimize heat loss, keeping the system efficient by preventing heat from escaping and reducing energy consumption.
- Control Systems: These systems monitor the temperature and adjust the heat output to keep everything running efficiently. Thermostats provide basic control, while digital controllers offer advanced programming and integration with existing systems.
- Power Distribution: A reliable power distribution network ensures that your heat trace system receives the right amount of energy to operate safely and effectively.
How MultiService Industrial Designs Heat Trace Systems
At MultiService Industrial, we believe in creating heat trace systems tailored to your unique needs. Here’s our step-by-step approach to ensure a perfect solution every time:
- Assessment: We evaluate your facility and identify key problem areas, whether it’s freeze protection or maintaining process temperatures.
- Heat Loss Calculations: Our team uses advanced tools to calculate heat loss and ensure that we’re accounting for factors like pipe material, ambient temperature, and insulation quality.
- Tailored Recommendations: Based on your needs, we recommend the best cable type, control system, and installation practices to guarantee long-term performance.
- Power Requirements: We design a power distribution system that meets your heat trace needs while ensuring safety and efficiency.
Heat Tracing Installation
A successful heat trace system starts with meticulous planning and precise installation. Following best practices during the setup phase ensures optimal performance and system longevity. Here’s how MultiService Industrial approaches installation to deliver reliable results:
- Preparation and Planning: Thorough site inspections address potential issues like moisture, surface irregularities, and accessibility, creating the foundation for a smooth installation process.
- Cable Installation Best Practices: Heat trace cables are securely attached to pipes using approved methods, preventing damage or loose fittings that could compromise system efficiency.
- Thermal Insulation Installation: Insulation materials are carefully applied to minimize heat loss, enhance system efficiency, and reduce energy consumption, ensuring long-term operational success.
Maintenance and Troubleshooting
Proper maintenance is essential to keeping your heat trace system operating efficiently and reliably. Routine inspections, performance monitoring, and timely repairs can prevent minor issues from escalating into major problems. Here’s how to maintain your system and how MultiService Industrial can help.
- Regular Inspections: Schedule periodic checks to spot any wear, damage, or potential issues early. Keep an eye on cables, connections, and insulation.
- Monitor Performance: Use control systems to track your heat trace system’s performance. Digital controllers make it easy to detect issues before they become problems.
- Keep the System Clean: Clear away debris and contaminants from cables and pipes, as these can hinder heat transfer and reduce system efficiency.
- Prompt Repairs: If you notice any damage or wear, address the issue immediately to prevent more serious complications.
- Partner with Experts: Regular maintenance and troubleshooting can be complex. Partnering with MultiService Industrial ensures your system receives expert care, minimizing downtime and extending its lifespan.
The Importance of Partnering with an Expert Contractor
When designing and implementing a heat trace system, selecting the right contractor is critical to ensuring optimal performance and long-term reliability. Facilities managers, plant engineers, project managers, and maintenance teams know the importance of making the right choice. Here’s what to consider when evaluating potential contractors and why MultiService Industrial stands out as the ideal partner.
Key Criteria for Selecting a Heat Tracing Contractor
- Experience & Qualifications
- Opt for a contractor with extensive experience in industrial heat tracing projects and a strong track record of success.
- Confirm they hold relevant industry certifications and follow strict safety and quality standards.
- Design & Engineering Capabilities
- A qualified contractor will offer advanced design and engineering services, such as heat loss calculations, system layout planning, and power distribution design.
- Ensure they leverage modern tools and materials to create efficient, customized solutions tailored to your facility’s needs.
- Comprehensive Range of Services
- Look for a contractor that provides end-to-end support, including consultation, system design, installation, and ongoing maintenance. This ensures seamless project execution and accountability at every stage.
Risks of Working With an Unqualified Contractor
Partnering with an inexperienced or unqualified contractor can lead to costly mistakes, inefficiencies, and even system failures. From incorrect cable selection to improper installation, these risks can compromise safety, reliability, and performance. Here’s how MultiService Industrial ensures your heat trace system is expertly designed, installed, and maintained to avoid these common pitfalls.
- Incorrect Cable Selection: Choosing the wrong cable can cause inefficient heating or system failure. At MultiService Industrial, we ensure that the cables selected are the perfect fit for your environment and temperature requirements.
- Improper Installation: Incorrect installation can damage cables or affect system performance. Our expert technicians follow best practices to ensure proper installation.
- Insufficient Maintenance: Neglecting maintenance can lead to system failures. We offer ongoing support to keep your system in top shape.
- Power Supply Issues: Inadequate power can disrupt your system’s functionality. We design robust power distribution systems to ensure reliable operation.
Why Choose MultiService Industrial?
Partnering with MultiService Industrial means choosing a company with unparalleled expertise, advanced technology, and a dedication to your success. Our team provides complete solutions for lasting results, from initial design to ongoing maintenance, supporting you throughout the entire process.
- Expertise You Can Trust: MultiService Industrial has years of experience delivering heat tracing solutions for industrial applications, backed by a proven track record of success.
- Tailored Solutions for Your Facility: We specialize in designing customized heat trace systems to address your unique challenges, ensuring maximum reliability and efficiency.
- End-to-End Support: From the initial consultation to installation and after-sales maintenance, we provide complete support, simplifying your project and giving you peace of mind.
Industries We Serve
Electric trace heat is used in any application where critical cold-sensitive equipment, raw materials, or products are exposed to freezing temperatures. It is widely used in:
- Oil and Gas: Preventing pipelines and storage vessels from slowing or freezing entirely in cold weather.
- Chemical Processing: Regulating chemical viscosity for smooth and safe processing and transport.
- Food and Beverage Processing: Maintaining food temperature to ensure quality and safety.
- Pharmaceuticals: Keeping ingredients at precise temperatures to protect the integrity of medications.
- Power Generation: Preventing condensation and freezing in power plant piping systems.
Ready to Optimize Your Heat Trace System?
Don’t let temperature challenges disrupt your operations. Contact MultiService Industrial today to discuss your heat tracing needs and discover why we’re the leaders in the field. Click the button below to schedule a free consultation with our experts and take the first step toward a smarter, more reliable heat trace solution.