Mechanical Insulation Design Guide
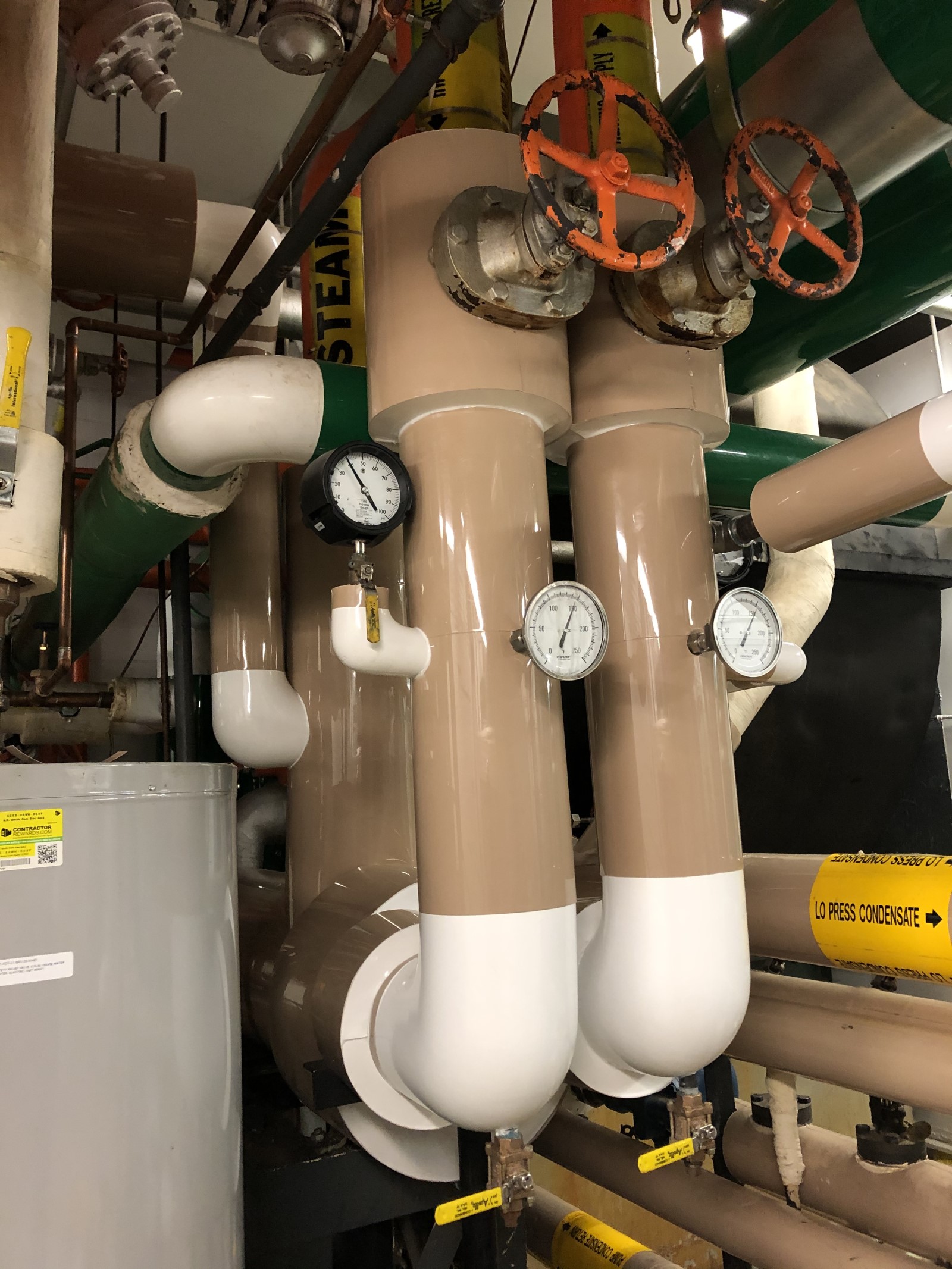
Mechanical insulation, when installed correctly, offers real gains in energy conservation, reduced carbon emission, safety, and cost reductions—all for a relatively modest investment in materials and installation. Our handy mechanical insulation design guide explains how to get the most out of your insulation install.
Often Applied, Rarely Engineered: Smart Mechanical Insulation Design
While many experts agree that better mechanical insulation is going to play a key part in the energy transition to a greener, cleaner economy, there’s less consensus on what good mechanical insulation looks like. As the National Mechanical Insulation Committee (NMIC) has noted: good insulation is often “applied, but rarely engineered.”
In other words, good intentions are no substitute for a thorough knowledge and proper application of mechanical insulation design practices needed to meet the energy conservation, emission reduction, and efficiency savings that this simpler and affordable environmental solution offers.
Our mechanical insulation design guide draws on recommendations by the NMIC and other expert groups to identify:
- What good mechanical insulation design is
- Key questions to consider in designing mechanical insulation
- Mechanical design best practices
- Critical steps to ensure good mechanical insulation design
Read on to learn how to make the most of mechanical insulation design at your plant, facility, building, or property.
1. What Is Mechanical Insulation Design?
Mechanical insulation is any material used to insulate stand-alone equipment or processes inside or outside a building, rather than the “envelope” insulation usually found built into the walls and ceilings of structures.
You’ll find mechanical insulation wrapped around ductwork and piping in attics and basements or possibly encasing hot water heaters and noisy generating equipment as well. In fact, mechanical insulation can be used anywhere that you need to manage sharp differences in energy levels to:
- Reduce heat or cooling loss
- Minimize expansion and contraction
- Lower noise levels
- Prevent burns or limit exposure to heat or cold
- Prevent or suppress fires
2. Key Mechanical Insulation Design Questions
For best results when you install mechanical insulation, you should understand the why, what, where, and how of your project.
Why Am I Insulating?
Properly insulating any equipment that is significantly warmer or cooler than its environment saves energy and helps to reduce both point source and overall carbon emissions. It also has clear, measurable bottom-line benefits for your company, including:
- Reduced overall energy costs
- Better heating and cooling performance and efficiency
- Reduced process variability
- Longer equipment lifedivs
What Am I Insulating?
You should focus your mechanical insulation installation on your most energy-hungry equipment or infrastructure. Mechanical insulation is also used to dampen noisy equipment and protect personnel from coming into contact with hot, sharp, or abrasive surfaces. Depending on your business, this could be:
- Boilers, furnaces, or cold storage
- Pipework supplying heated or chilled feedstocks
- HVAC ductwork, hot water heaters, and heat pumps
- Generators and exhaust systems
- High speed/ high-friction industrial equipment
Where Am I Insulating?
The location of your equipment will influence both your insulation design and the material you choose. For example:
- Is the equipment outdoors? What are local weather conditions like?
- What are the differences between the insulated and ambient temperatures?
- Is the equipment in a high-traffic area or close to places where people live, work, or eat?
- How much usable space is there around the equipment?
How Am I Insulating?
What insulation materials or systems should you choose, based on the above considerations and your budget or other constraints? Any material that holds a lot of enclosed air spaces relative to its volume can be used as a mechanical insulator. For this reason, mechanical insulation products tend to be made from materials that are:
- Cellular, such as expanded plastics and closed-cell foams like polyisocyanurate
- Fibrous, such as fiberglass or mineral wool
- Flaked, such as vermiculite or other processed minerals
- Granular, such as perlite or calcium silicate
- Reflective, such as silver-painted insulation panels
Mechanical insulation products come in different forms for different applications, including:
- Panels and tiles for installation around equipment
- Rolls of woven or expanded material for wrapping pipes or ducts in tight spaces
- Loose or granular products for filling up irregular spaces
- Sprayable expanding foam for insulating inaccessible places
Specific information on the properties of common insulating materials can be found here.
Mechanical Design Best Practices
Now that you know what you want to achieve by insulating your equipment, consider the following best practices as you implement your project.
Insulation Thickness
Be sure that the thickness of your material provides effective insulation based on the operating temperature, the ambient temperature, and the desired heat loss or gain. The greater the temperature difference, the thicker the insulation that will be required. Be sure, for instance, that your insulation will provide freeze protection in the event of a system failure during cold weather.
Insulating Material
Along with its insulating properties, your material should also be resistant to corrosive or abrasive environments while protecting personnel from heat and sharp corners. It should also be moisture resistant and fire rated.
Condensation Control
Along with moisture resistance, your insulation should be designed to manage condensation resulting from sharp temperature differences. Condensation can lead to:
- Water drips that pose a slip hazard
- Mold and mildew growth
- Corrosion of metal parts
Ideally, your system needs to prevent condensation on the outside surface of insulating material while also stopping moisture from seeping into the material itself. Along with its insulating properties, the NMIC provides specific recommendations for the thickness of your material in order to prevent or minimize condensation.
Engineer Your Insulation
Correctly installed insulation should avoid both gaps or voids as well as compressions where heat can be exchanged. Choose a material with the best insulating properties you can afford as well as a form that suits the space you are working in. For example, choose roll or spray-on insulation for pipes and granular fills for irregular spaces.
Regular Maintenance
Insulation is a process, not an event. Be sure to inspect and maintain your insulation at regular intervals to ensure it is performing as required. Look for tears or breaks, animal damage, and freeze-thaw issues as well as mold, rust, or stains from moisture accumulation.
Accessibility
Remember that equipment needs to be accessed regularly for maintenance and repair. You will extend the life of your insulation as well as your equipment by making sure critical components can be inspected and items like furnace filters, flow meters, oil sumps, and pipe cleanouts can be reached easily.
Fire Protection
Your insulation should enhance fire safety and protection in your property, not make it worse. Choose rated materials that are fire and flame resistant, especially around electrical or gas equipment and machinery. Ensure fire suppression systems are installed and working properly.
Good Mechanical Design: 8 Critical Steps
Based on these recommendations, we suggest following these steps to ensure your mechanical insulation design is as effective as possible.
- Determine the equipment operating temperature you need to maintain. This will guide your choice of insulating material.
- Determine your required thermal resistance. Review material specifications to determine how much heat or cold you can afford to lose. Take ambient temperature into account.
- Choose an appropriate insulating material based on thermal performance, moisture resistance, durability, fire rating, and shape of the equipment and the space around it.
- Add a vapor barrier: Where temperature loss is steep or moisture levels are high, use an extra vapor barrier on the warm side of the insulation to minimize condensation.
- Build-in accessibility: Make sure meters, panels, inspection certificates, filters, cleanouts, sumps, separators, and other access points remain accessible.
- Design for safety: Make sure your insulation protects people from cuts, bumps, and slips and does not add any additional hazards. Also ensure that fire suppression systems work.
- Install: With all the planning completed, it’s time to spray, wrap, glue, and fill your way to better insulation. Make your job easier by choosing materials that suit the available space.
- Inspect, maintain, replace: Regularly inspect your insulation to make sure it remains in place, is undamaged, and continues to do its job. Repair and replace as needed.
For Best Results, Talk to an Expert
Mechanical insulation is not as glamorous as electric cars or advanced carbon capture technologies. But experts believe that simply improving efficiency by properly insulating existing buildings and equipment will play a huge role in the energy transition, and at a fraction of the cost of most other solutions.
Effective insulation allows you to reduce your carbon footprint while cutting your energy costs and prolonging the life of your critical equipment, so it’s worth taking the time to ensure your mechanical insulation design is sound.
Consult industry resources, such as the Whole Building Design Guide. For maximum confidence, efficiency, and return on investment, however, you should consider talking to an industry expert like Richmond-based MultiService Industrial.
We offer specialist mechanical insulation consultations and installation services. Serving both commercial and industrial facilities, we design mechanical insulation solutions to keep heat where it belongs, prevent condensation, improve safety, and cut energy bills. Talk to us today about the energy-saving opportunities that already exist in your buildings, including:
- Pipe insulation
- Chilled water pipe/chiller pipe insulation
- Mechanical room equipment sound insulation
- Storage tank insulation
- HVAC boiler and furnace insulation
- Ductwork insulation
At MultiService Industrial, our highly experienced team is ready to deliver fully engineered solutions to your mechanical insulation design challenges while meeting the highest standards.
Click below to learn more or to arrange a consultation.