6 Problems With Industrial Insulation
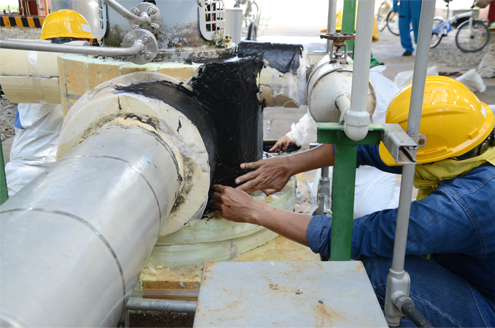
Insulation reduces the rate at which heat flows from hot to cold. In industrial environments, it reduces energy costs, enables more precise process control, and helps keep workers and others close by from harm. If the insulation is defective, it won’t perform these functions to the level required, which can mean unexpected shutdowns and repair bills.
Industrial insulation problems take many forms. They range from seemingly insignificant to very obvious failures. Here are the top six to watch for.
1. Wrong insulation for the application
Insulation comes in many forms, and a complete installation usually incorporates several components. Materials must be appropriate to the application.
Industrial insulation contractors lacking industry-specific experience may pick the wrong insulating material, vapor barrier, or sheathing, either by accident or choice. They may not appreciate all the details of the application, or they may choose inexpensive materials because they bid low to win the job.
Some points to consider are the temperature difference or delta T being insulated, whether the insulation is outdoors or indoors, how much space is available, and whether there are any particular environmental factors at play. These dictate the type and thickness of material needed.
2. Too little, or too much, insulation
A common mistake is thinking more insulation is better. After a certain thickness diminishing returns set in, the additional cost exceeds the benefits. However, insufficient insulation, perhaps as a cost-saving measure, leads to increased heat loss and all the problems that go with that.
For buildings, a good way to determine how much insulation is needed is to look at the R-value specified for the geographical installation area by the International Energy Conservation Code (IECC). The R-value of an insulation material indicates how well it resists heat flow. It’s measured in units of (ft2 x °F x hour)/BTU and higher numbers mean better performance.
To insulate industrial equipment like a cryogenic system or a furnace, consider calculating a target R-value that will optimize insulation and operating costs.
3. Faulty installation
Insulation almost always requires a vapor barrier and an outer sheath. These prevent heat transfer and moisture penetration. Joints in the insulation must be sealed with care to avoid this latter problem, preferably with pressure-sensitive adhesive tape rather than staples. It’s important to limit the use of staples as these provide openings for moisture and corrosion. Joints in sheathing should be caulked.
In addition, insulation must be shaped and fitted at elbows and tees, around valves, and where pipes exit tanks or other vessels. Insufficient attention to these details may lead to costly industrial insulation problems.
When insulation is removed for maintenance or repair work it must be replaced or refitted to the same standard it was originally installed.
Faulty installation often goes hand-in-hand with incorrect material selection. For example, using high-density expanded polystyrene (EPS) when polyisocyanurate (ISO / PIR) would be a better choice.
4. Moisture
When insulation gets wet it loses virtually all of its ability to prevent heat flow. It can also cause corrosion under the insulation around pipes and storage vessels, even those fabricated from stainless steel. If the moisture subsequently freezes it can cause extensive damage.
Moisture gets into insulation in three ways. If the sheathing is damaged or improperly installed, this leaves pathways for water to penetrate from outside. It can also result from condensation when humid air comes into contact with the cold surfaces of pipes and tanks. This is a common problem with chilled water lines and is prevented by the correct installation of an appropriate vapor barrier.
The third way in which insulation gets wet is if it is installed over wet surfaces, as would be the case if the work was done during bad weather or a period of high humidity.
5. Contamination/corrosion
“Contamination” in this context refers to pollutants that could attack the sheathing or insulating material. Chemical leaks and airborne gases are possible culprits, as are other materials used in industrial processing operations such as lime.
An experienced industrial insulation contractor will avoid such problems by carrying out a thorough assessment of the environment before selecting materials for the application.
6. Damage
Damaged sheathing lets moisture in and allows heat to flow. Damage often results from pipework on ducting being climbed on to reach parts of a process plant or other equipment. It can also result from an accident such as a fork truck being driven into or scraping alongside pipes or storage tanks.
Industrial insulation problems due to damage are minimized by performing regular inspections and insulation maintenance. In some situations, such as where steam pipes are insulated, thermal imaging may help identify leaks or ineffective insulation.
Where possible, install appropriate guards or barriers that prevent sheathing from being damaged.
Work With a Professional Contractor to Avoid Industrial Insulation Problems
Insulation should be thought of as an essential component of industrial equipment and buildings: if it doesn’t perform as needed it will affect costs and possibly also product quality and worker safety.
Industrial insulation problems are prevented by correct material selection and installation, coupled with regular inspection and professional repair when needed. MultiService has experience with all types of industrial insulation and can help you avoid downtime for insulation repair.
To learn more about our services, click below.